The Need for Flameproof Enclosures
The ‘Ex d’ type of protection, known as “flameproof enclosure” protection, is widely used in hazardous areas where there is a risk of explosions due to the presence of flammable gases, vapours, or dust. This robust and simple technology is crucial for ensuring protection of personnel, infrastructure, neighbouring businesses, and even casual passersby, in surrounding environments.
How ‘Ex d’ Protection Works
Containment of Explosion
‘Ex d’ protection contains any explosion within the enclosure. If a flammable gas or vapor inside the enclosure ignites, the explosion is confined, preventing it from spreading to the surrounding atmosphere.
Pressure-Resistant Enclosure
The enclosures are designed to withstand the pressure generated by an internal explosion. They are robustly built to ensure that no part of the explosion can breach the enclosure and reach the outside environment.
Cool Flames
The enclosure has joints and gaps designed to cool the escaping gases from an internal explosion. These gaps allow the hot gases to cool down to a temperature below the ignition point of the surrounding flammable atmosphere before they escape.
Strict Design Standards
Enclosures must meet stringent standards and undergo rigorous testing to ensure they can handle the pressure of an internal explosion and effectively cool escaping gases. They are made from durable materials like cast aluminum, stainless steel, or cast iron.
An example of such a durable product is the HMI 800/900-Z1 Industrial Monitor, designed to ensure longevity and safety in hazardous environments. These monitors are certified for use in hazardous areas, utilizing the Ex d protection method, which simplifies maintenance and enhances safety. Designed for applications such as CCTV in hazardous locations, the HMI 800 and 900-Z1 offer versatile input options including DVI-D, VGA, or Composite directly driven input signals. They also support extension over CAT5 or Fiber for remote operation, allowing for flexible placement of the display in safer areas while the video source remains in the hazardous location.
800_900Z1
HMI 800/900-Z1 Industrial Monitor
Areas Covered by ‘Ex d’ Protection
Hazardous Locations
Used for housing electrical components such as motors, switches, transformers, and instrumentation in hazardous areas, ensuring these components do not ignite the surrounding atmosphere.
Another application of Ex d protection is in lighting. The Nightsearcher Titan SafAtex AC + 24V Pendant Floodlight exemplifies Ex d protection with its high-strength aluminum housing and explosion-proof design. It is certified for Gas Zone 1 and Dust Zone 21, making it suitable for various hazardous locations. This floodlight features ultra-bright LEDs and a shock and vibration-resistant tempered glass, ensuring reliable performance in demanding conditions. Its adjustable bracket allows for versatile installation, and the built-in surge protection further enhances its durability. The Titan ATEX AC Floodlight is perfect for areas requiring robust and reliable lighting, such as oil rigs, chemical plants, and other industrial settings.
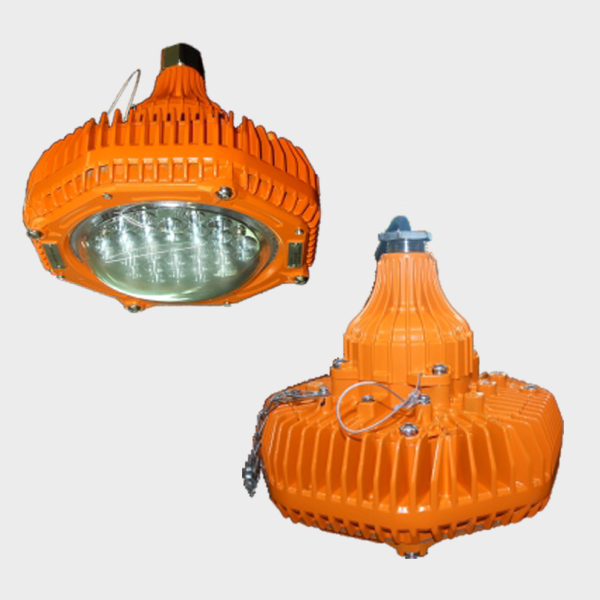
Atex Titan Pendant Flood Light 2
SafAtex AC + 24V Pendant Floodlight

Portable WL Main
Rechargeable Portable Worklight
Additionally, the Nightsearcher Titan Rechargeable Portable Worklight offers a portable lighting solution with Ex d certification for Zones 1 and 21. Its rugged design includes an abrasion and corrosion-resistant aluminum housing, making it perfect for mobile applications in hazardous areas. With up to 2100 lumens output and a long battery life, this floodlight provides essential lighting for maintenance tasks and emergency situations. Available with magnetic feet or a stainless steel stand, it offers flexibility in deployment. The SAFATEX FLR’s high output and durable construction make it a critical tool for ensuring safety in explosive environments.
Importance of ‘Ex d’ Protection
Safety
Protects personnel and equipment by containing explosions within the enclosure, minimizing the risk of fire or secondary explosions in the surrounding area.
Compliance
Ensures compliance with international safety standards and regulations for equipment used in hazardous areas, facilitating global operations and installations.
Making Enclosures Flameproof
Design and Material
Enclosures are made from materials like cast aluminium, stainless steel, or cast iron, known for their strength and durability. Precision manufacturing includes machined joints, gaskets, and threaded covers to ensure they can withstand internal explosions.
Flame Path Design
The joints and gaps between parts are designed to create long, narrow flame paths. These paths cool the escaping gases below ignition temperature before they exit the enclosure. Threaded joints or flanges are meticulously machined to ensure they are tight enough to contain the explosion but still allow heat dissipation.
Pressure Resistance
Enclosures are designed to withstand the peak pressure from an internal explosion. The walls are thick, and the construction is sturdy to handle these forces.
Testing and Certification
Initial Testing
Flameproof enclosures are filled with a flammable gas mixture and then ignited internally to ensure they can contain the explosion. As part of this, they are placed inside a plastic bag with an identical atmosphere to the one inside the enclosure. The whole setup is placed in an explosion proof testing unit and the internal gas is ignited. As long as the explosive atmosphere in the bag surrounding the unit doesn’t ignite, the test is considered successful.
Pressure Testing
Flameproof enclosures undergo hydrostatic testing, where they are filled with water and pressurised to test their strength and integrity without the risk of fire. Standard testing means they are pressurised to 1.5 times their top rating to assure they have margin above that upper limit for extra safety. Explosionproof enclosures are tested similarly, but to four times their maximum flameproof pressure rating. They require a much greater resistance for an explosionproof label.
Temperature Measurement
During explosive tests, the surface temperature of the enclosure is also monitored. Certification requires that it doesn’t exceed safe levels that could ignite the surrounding atmosphere.
Certification Standards
Enclosures are tested to meet international standards such as IEC 60079-1 (International Electrotechnical Commission) or UL 1203 (Underwriters Laboratories) for explosion-proof equipment. Beyond that, independent certification bodies perform rigorous testing and certify that the enclosures meet all safety standards.
Failure Rates and Reliability
Low Failure Rates
Due to the rigorous testing and high standards, failure rates for certified ‘Ex d’ enclosures are very low. The continuous quality control during manufacturing ensures that each enclosure meets the required specifications.
Causes of Failure
Failure can occur if enclosures are not properly maintained, such as not securing bolts tightly or failing to replace damaged gaskets. Physical damage or corrosion can compromise the integrity of the enclosure. Painting or incorrect application of corrosion protection on the flame joins can cause temperature and pressure build up as the gap cannot properly cool an internal explosion.
Reliability
Enclosures should be regularly inspected and maintained to ensure they remain in good condition and continue to provide protection. As well, it is necessary to ensure that enclosures are appropriate for the specific environmental conditions they are used in (e.g., corrosion-resistant materials in marine environments) to assure reliability.
Room for Improvement
Improving “Ex d” standards and ensuring continuous safety advancements in hazardous areas is a critical focus for many organisations and researchers. Here are several ways these standards can be improved and some ongoing efforts in this direction:
Enhanced Materials
Developing stronger, lighter, and more corrosion-resistant materials with ordinary metallurgical processes will improve the durability and lifespan of flameproof enclosures. Utilising material sciences and nanotechnology to create materials with superior heat resistance and strength will likely contribute even more.
Design Innovations
Improving the design of flame paths to enhance cooling efficiency and further reduce the risk of external ignition will continue. Isolating individual enclosures is already happening with some being designed to surround the connections (once made) with a liquid substance that is poured into the box, which then solidifies. Nowadays we still use glands to form a gasproof seal between wires coming into an enclosure. Glands expand or seal within the connection point, effectively isolating things that spark (switch, motors, etc.) from the external vapours. Creating more modular designs is another step that will allow for easier maintenance and repairs without compromising safety. Units can be swapped wholesale without opening them within the environment, and if practical, serviced elsewhere.
Advanced Manufacturing Techniques
3D printing and other advanced manufacturing techniques will allow us to produce more precise and complex enclosure designs. Similarly, implementing automated inspection and quality control processes will ensure consistent and defect-free production. We’re already printing 3D metals and developments like Nanovate N1210 Alloy allow us to coat a ping pong ball to a thickness of 300 µm (three human hairs) which then resists 232,000 psi—many times stronger than steel…
Improved Testing Methods
Developing real-time monitoring systems to continuously assess the condition of enclosures and detect any potential failures before they occur is a good maintenance practice. Utilising advanced simulation tools to model explosions and stress scenarios more accurately, will also lead to better design optimisation.
Smart Enclosures
Embedding sensors within enclosures to monitor temperature, pressure, and structural integrity, will provide early warnings of potential issues. Another innovation is connecting enclosures to the Internet of Things (IoT) for remote monitoring and predictive maintenance.
Ongoing Efforts and Research
Standards Organisations
The International Electrotechnical Commission (IEC) and the International Organisation for Standardisation (ISO) continuously review and update safety standards based on new research and technological advancements. Organisations like UL (Underwriters Laboratories) in the US and ATEX (Atmosphères Explosibles) in Europe are actively involved in improving explosion protection standards.
Research Institutions
Many universities conduct research on materials science, explosion dynamics, and industrial safety, contributing to the development of improved standards. Collaborations between academia and industry help translate research findings into practical applications.
Industry Initiatives
Companies in the oil and gas, chemical, and mining industries invest in research and development to enhance safety measures, including ‘Ex d’ protection. Groups like the Hazardous Area Protection Group work to share knowledge and best practices across different sectors, driving improvements in safety standards.
Conclusion
Improving ‘Ex d’ standards involves a multifaceted approach, incorporating advancements in materials, design, manufacturing, and testing. Continuous efforts from standards organisations, research institutions, and industry players are crucial in driving these improvements. As technology progresses, we can expect to see more sophisticated and reliable flameproof enclosures that provide even greater protection in hazardous environments.